Membrane Roofing: Your Ultimate Guide to Durable Roofing Solutions
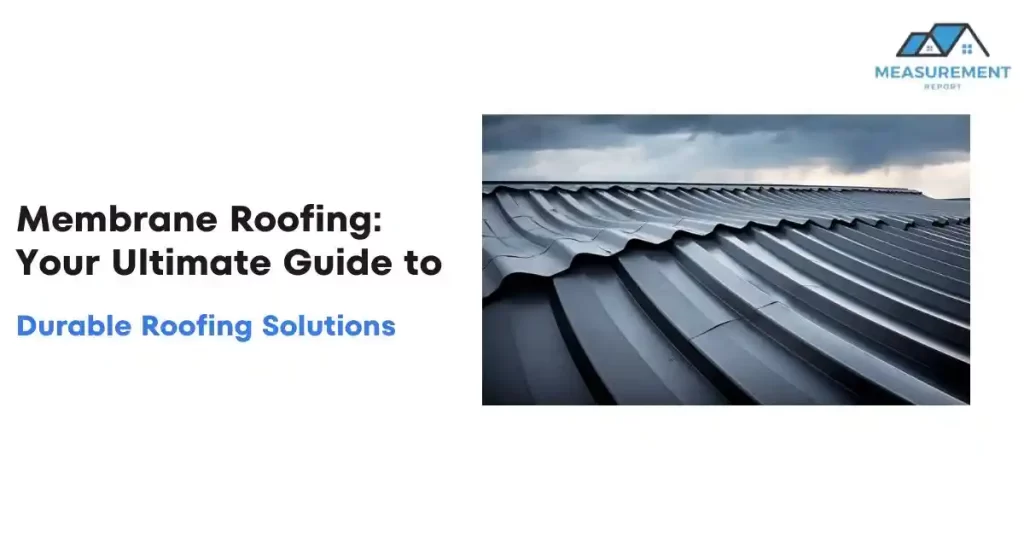
Membrane roofing stands as a pinnacle of modern roofing technology, embodying both innovation and practicality in the world of construction. At its core, membrane roofing refers to a type of roofing system that is predominantly used for buildings with flat or low-slope roofs. This technology involves the use of synthetic membranes, which are specifically engineered to provide a watertight seal over the roof, thereby effectively protecting the structure from water damage and the elements.
The importance of membrane roofing in contemporary construction cannot be overstated. As architectural designs have evolved, the demand for roofing solutions that accommodate flat or low-angled structures has significantly increased. Membrane roofing not only meets this demand but also offers a range of benefits that traditional roofing materials struggle to match. Its adaptability, durability, and energy-efficient properties make it an ideal choice for a wide array of buildings, from commercial and industrial complexes to residential properties.
In an era where sustainability and longevity are key concerns in construction, membrane roofing emerges as a frontrunner. Its ability to withstand harsh environmental conditions, coupled with its minimal maintenance requirements, positions it as a future-oriented solution. This roofing type not only ensures the longevity of the buildings it graces but also aligns with the increasing environmental consciousness in building practices.
As we delve deeper into the intricacies of membrane roofing, we will explore its various types, installation processes, cost-effectiveness, and maintenance, providing a comprehensive understanding of why it has become a preferred choice in modern roofing solutions.
Understanding Membrane Roofing
What is Membrane Roofing?
Membrane roofing is a specialized roofing system, primarily used for buildings with flat or low-slope roofs. This roofing type employs continuous, synthetic membranes that cover the entire roof area, creating a seamless and waterproof barrier. These membranes are typically made from modified bitumen, thermoset materials (like EPDM), or thermoplastics (such as PVC and TPO). The essence of membrane roofing lies in its ability to provide a robust, flexible, and long-lasting cover that is adept at resisting environmental extremes and preventing leaks.
The basic concept of membrane roofing revolves around its ability to flex and move with the building structure while maintaining its integrity and waterproofing capabilities. Unlike traditional pitched roofs that rely on gravity to shed water, flat or low-slope roofs require this kind of impermeable barrier to protect the building from water pooling and infiltration.
Brief History and Evolution
The history of membrane roofing dates back several decades, where it began as a response to the limitations of conventional roofing materials like asphalt and gravel on flat roofs. Initially, built-up roofs (BUR) – layers of tar and gravel – were the standard solution for flat roofs, but they had limitations in terms of weight, flexibility, and susceptibility to leaks.
The evolution of membrane roofing began with the introduction of synthetic materials in the mid-20th century. The first major breakthrough was the development of EPDM (ethylene propylene diene monomer) in the 1960s, a type of synthetic rubber known for its durability and resistance to weathering. This was followed by other innovations like PVC (polyvinyl chloride) and TPO (thermoplastic olefin), which offered improved characteristics such as better heat resistance, flexibility, and environmental friendliness.
Over the years, membrane roofing has continually evolved, incorporating advanced technologies to enhance performance. Modern membranes often include features like UV resistance, energy efficiency, and increased longevity. They have become more eco-friendly, with some materials being recyclable and others engineered to improve a building’s energy efficiency.
This progression from basic built-up roofs to sophisticated membrane systems reflects a significant advancement in roofing technology. Today, membrane roofing stands as a testament to the industry’s commitment to innovation, sustainability, and providing effective solutions to the unique challenges presented by flat and low-slope roofs.
The Different Types of Membrane Roofing
EPDM Roofing Material
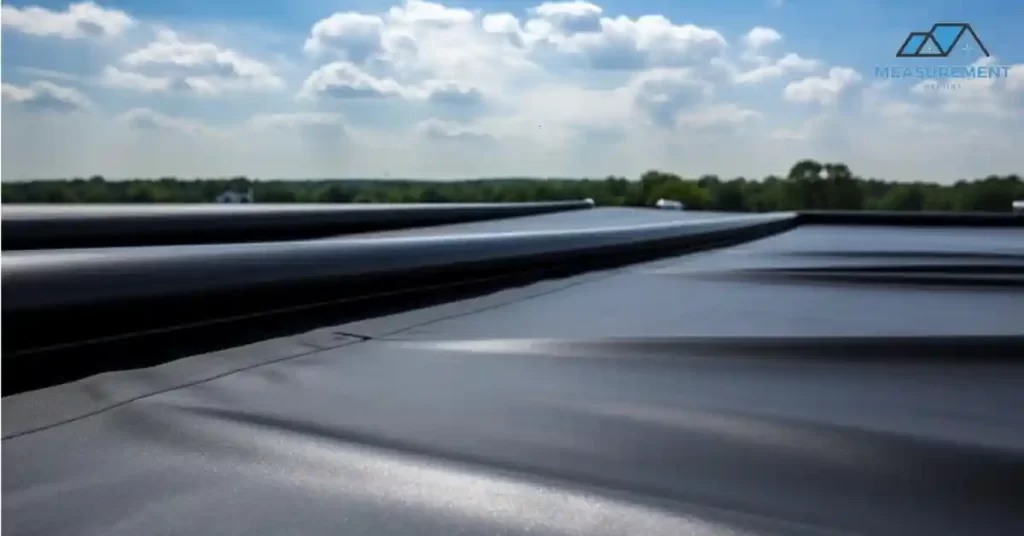
Ethylene Propylene Diene Monomer (EPDM) roofing is a type of thermoset membrane made from synthetic rubber. Renowned for its remarkable durability and versatility, EPDM is a popular choice for both residential and commercial flat roofs. One of its key characteristics is its exceptional resistance to UV rays, ozone, and weathering. EPDM roofs are usually black, although white-coated versions are available for enhanced energy efficiency. The installation process can vary, involving either ballasting, mechanical attachment, or fully adhered systems. Its resilience to temperature fluctuations and ability to handle thermal shock makes EPDM a go-to material for many roofing professionals.
TPO Roofing Material
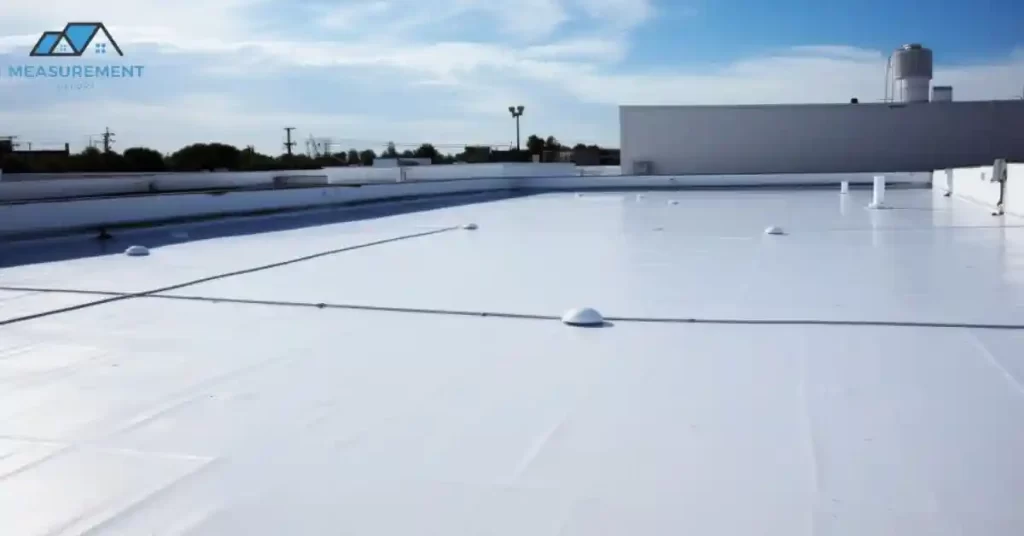
Thermoplastic Polyolefin (TPO) is a type of thermoplastic membrane that has gained popularity for its energy efficiency and ease of installation. TPO membranes are typically white, reflecting sunlight and helping reduce cooling costs in warmer climates. These roofs are known for their heat-welded seams, which provide superior strength and make the membrane virtually leak-proof. TPO combines the durability and performance of EPDM and PVC roofs but often at a more cost-effective price point. It is also environmentally friendly, being 100% recyclable and free from chlorine.
PVC Roofing Material
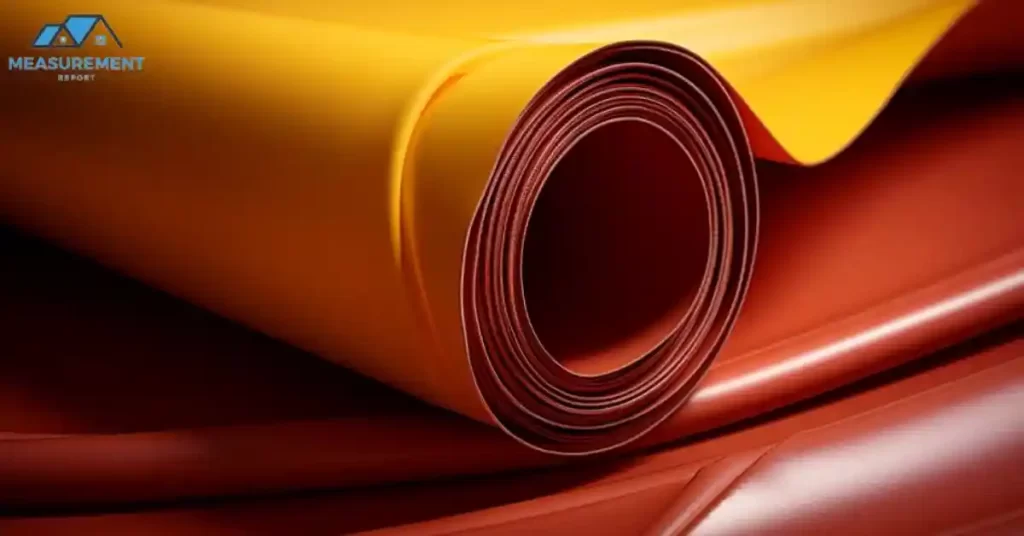
Polyvinyl Chloride (PVC) roofing membranes are another category of thermoplastic roofing materials. PVC roofs stand out for their resistance to chemicals, oils, and other potentially harmful substances, making them ideal for restaurants and other businesses that emit fats or oils through ventilation systems. These roofs are also highly resistant to fire and punctures. Like TPO, PVC roofs are heat-welded, resulting in strong, watertight seams. Additionally, they are available in a variety of colors and can be made more energy-efficient with cool-roof coatings.
Additional Types
- Modified Bitumen: This type blends traditional asphalt roofing with modern polymer modification. Modified bitumen roofs are easy to repair and maintain, and they offer enhanced flexibility and durability compared to traditional asphalt roofing.
- Liquid-Applied Membranes: These are applied in liquid form and cure to form a seamless, monolithic membrane. They are often used for repair or as a top coat for existing roofs due to their versatility and adaptability to complex geometries.
- Green Roofing Systems: While not a membrane in the traditional sense, these systems often use membrane roofing as a base layer to support vegetation, contributing to urban heat island reduction and improving insulation.
Each of these types of membrane roofing has its unique strengths and ideal applications, allowing for tailored solutions based on specific needs such as climate, building use, and budget.
Comparing Membrane Roofing with Traditional Materials
Membrane Roofing vs. Traditional Roofing
Membrane roofing systems present a stark contrast to traditional roofing materials, especially in their application, performance, and suitability for different roof types. Traditional roofing, which often includes materials like asphalt shingles, metal, and tile, is predominantly used in pitched or sloped roof designs. These materials rely on overlapping or interlocking designs to shed water effectively. In contrast, membrane roofing is specifically engineered for flat or low-slope roofs, where water shedding is not as straightforward.
Membrane vs. Asphalt Shingles
Asphalt shingles, a staple in residential roofing, differ significantly from membrane roofing in both structure and application. While shingles are suitable for sloped roofs due to their ability to shed water quickly, membrane roofing excels on flat or low-slope roofs where water pooling is a concern. The continuous, seamless nature of membrane roofing provides a watertight seal that shingles cannot match on these roof types. Additionally, membrane roofs tend to have a longer lifespan and require less maintenance than asphalt shingles, although the initial installation cost can be higher.
Advantages Over Other Roofing Materials
Membrane roofing offers several advantages over traditional materials:
- Durability: Membrane roofs are highly resistant to tears, punctures, and weathering.
- Flexibility: They can accommodate building movement and temperature fluctuations better than rigid materials.
- Energy Efficiency: Many membrane materials reflect sunlight and heat, contributing to lower cooling costs.
- Waterproofing: Membrane roofing provides superior waterproofing capabilities, essential for flat or low-slope roofs.
- Ease of Maintenance: These roofs are generally easier to inspect, repair, and maintain.
When to Choose Membrane Roofing
Membrane roofing is an ideal choice in several scenarios:
- For Flat or Low-Slope Roofs: Where traditional shingles or tiles would not be effective.
- In Climate-Exposed Areas: Where buildings are subjected to extreme weather conditions.
- For Energy Efficiency Needs: In areas where reducing cooling costs is a priority.
- For Commercial Buildings: Especially for larger roofs where the seamless nature of membranes offers substantial advantages in waterproofing and maintenance.
- When Seeking Long-Term Solutions: Given their durability and longevity, membrane roofs are an excellent long-term investment for many buildings.
Selecting the right roofing material involves considering factors such as roof design, climate, budget, and specific building needs. Membrane roofing, with its unique set of advantages, has become a favored choice for many modern construction projects, particularly where flat or low-slope roofs are involved.
Installation and Cost
Installation Process of Membrane Roofing
The installation of membrane roofing is a specialized process that varies slightly based on the type of membrane chosen (EPDM, TPO, PVC, etc.). However, there are common steps that are generally followed to ensure a successful and long-lasting installation.
Step-by-Step Guide to Membrane Roofing Installation
- Roof Inspection and Preparation: The first step involves a thorough inspection of the existing roof structure. Any damage or issues, such as trapped moisture or uneven surfaces, must be addressed. The roof is then cleaned and prepared for installation.
- Installing Insulation (Optional but Recommended): Often, a layer of insulation is added to improve energy efficiency. This layer is typically installed directly onto the roof deck.
- Membrane Laying: The membrane material is rolled out over the insulation or roof deck. For larger roofs, several rolls of membrane might be used, and they must be carefully aligned.
- Seaming: If multiple membrane sheets are used, they are seamed together to form a continuous, watertight layer. The method of seaming varies; for instance, EPDM membranes might be adhered with a special adhesive, while TPO and PVC membranes are typically heat-welded.
- Attaching the Membrane: The membrane can be attached to the roof deck using mechanical fasteners, adhesives, or ballasting (weighing down with a heavy material, often stone).
- Detailing: The final step involves finishing details such as installing flashing around roof penetrations, edges, and corners to ensure complete waterproofing.
- Inspection and Testing: Once installed, the roof should be inspected and tested for any leaks or flaws in the installation.
Finding the Right Contractor
Choosing a qualified and experienced contractor is crucial for the successful installation of a membrane roof. Here are a few tips for finding the right contractor:
- Check for Licensing and Insurance: Ensure the contractor is licensed to work in your area and carries adequate insurance.
- Experience with Membrane Roofing: Look for a contractor with specific experience in the type of membrane roofing you’re installing.
- References and Portfolio: Ask for references or a portfolio of past projects.
- Warranty and After-Service: Inquire about the warranty offered on the installation and the contractor’s policy for after-service in case of issues.
- Cost Estimates: Get detailed written estimates from several contractors for comparison. Remember, the lowest bid is not always the best choice if it compromises on quality.
The cost of membrane roofing installation varies depending on factors like the type of membrane, roof size, complexity, and regional labor costs. While the initial investment might be higher than some traditional roofing materials, the long-term benefits and lower maintenance costs often make membrane roofing a cost-effective solution in the long run.
Per Square Foot Installation Cost
The installation cost of membrane roofing per square foot can vary widely based on several factors, including the type of membrane material chosen, the complexity of the roof, geographic location, labor costs, and any additional features or requirements of the project. Here is a general breakdown of the costs associated with different types of membrane roofing:
- EPDM Roofing: EPDM is often one of the more affordable options. The cost per square foot for EPDM roofing installation typically ranges from $3.50 to $7.00. This includes the cost of materials and labor. EPDM’s affordability, coupled with its durability, makes it a popular choice for those looking for a balance between cost and performance.
- TPO Roofing: TPO roofing costs are comparable to EPDM, generally falling in the range of $3.50 to $8.00 per square foot. TPO’s energy-efficient properties can make it a more cost-effective choice in the long term, especially in climates where reducing cooling costs is a priority.
- PVC Roofing: PVC membrane roofing usually falls on the higher end of the spectrum, costing between $6.00 and $9.00 per square foot. This cost reflects its superior resistance to environmental factors like chemicals and oils, as well as its long lifespan and low maintenance requirements.
- Other Factors Affecting Cost:
- Roof Size and Complexity: Larger and more complex roofs require more materials and labor, increasing the overall cost.
- Insulation and Decking: If the roof requires new insulation or decking, this will add to the cost.
- Removal of Existing Roofing: If the old roofing material needs to be removed and disposed of, this can also increase the project’s cost.
- Geographical Location: Labor and material costs can vary significantly depending on the location.
It’s important to get multiple quotes from reputable contractors to understand the specific costs for your roofing project. Each roofing project has unique aspects that can influence the final price, so these figures should be used as a general guide. Additionally, investing in a quality installation can result in fewer repairs and a longer lifespan for the roof, which can lead to cost savings over time.
Lifespan of Membrane Roofing
Average Lifespan and Factors Affecting It
The longevity of membrane roofing is one of its most appealing attributes, with lifespans that can vary significantly based on the type of membrane, installation quality, environmental conditions, and maintenance practices.
- EPDM Roofing: EPDM roofs are known for their durability, typically lasting between 20 to 35 years. The quality of the installation and the thickness of the membrane (which can vary) are crucial factors that influence its lifespan.
- TPO Roofing: TPO membranes generally have a lifespan ranging from 15 to 25 years. The lifespan can be influenced by factors like the quality of the welding, exposure to UV rays, and the type of reinforcement used in the membrane.
- PVC Roofing: PVC roofs can last between 20 to 30 years. Factors like the formulation of the PVC, the quality of the plasticizers used, and the roofing system’s overall design play a significant role in determining its longevity.
Factors Affecting Lifespan
Several factors can impact the lifespan of a membrane roof:
- Installation Quality: Proper installation by experienced professionals is crucial for maximizing the lifespan of the roof. Poorly welded seams, improper attachment, and inadequate detailing around roof penetrations can all shorten the roof’s life.
- Maintenance: Regular maintenance, including inspections and prompt repairs, can significantly extend a roof’s lifespan. Membrane roofs should be inspected at least once a year and after major weather events.
- Climate and Environmental Exposure: The local climate can have a considerable impact. For instance, roofs in areas with extreme temperature fluctuations, heavy rainfall, or high UV exposure may experience accelerated aging.
- Roof Design and Drainage: Effective drainage is critical for membrane roofs, especially on flat surfaces. Poor drainage can lead to water pooling, increasing the risk of leaks and material degradation.
- Foot Traffic: Excessive foot traffic can cause wear and tear on a membrane roof, particularly if the roof is frequently accessed for maintenance of equipment like HVAC systems.
- Material Quality: Higher quality materials, though more expensive upfront, can offer better durability and resistance to environmental factors, thus extending the roof’s life.
By understanding these factors and addressing them through proper selection, installation, and maintenance, the lifespan of a membrane roof can be maximized, ensuring it provides a reliable and cost-effective roofing solution for many years.
Warranty and Quality Aspects
What to Look for in a Membrane Roofing Warranty
When selecting a membrane roofing system, understanding and comparing the warranties offered is crucial. A comprehensive warranty can provide peace of mind and protection against potential defects or failures. Here are key aspects to consider in a membrane roofing warranty:
- Length of Warranty: The duration of the warranty can vary, typically ranging from 10 to 30 years. Longer warranties may indicate higher confidence in the product’s durability.
- What’s Covered: Carefully review what the warranty covers. Some warranties may cover only the material, while others might include labor costs for repairs.
- Prorated vs. Non-Prorated: Understand whether the warranty is prorated (decreases in value over time) or non-prorated (offers full coverage throughout the term).
- Exclusions and Limitations: Pay attention to what is not covered. Common exclusions might include damage due to improper installation, extreme weather events, or failure to perform regular maintenance.
- Transferability: Some warranties are transferable to new property owners, which can be a selling point if you plan to sell your property.
- Maintenance Requirements: Some warranties require regular maintenance and inspections for the warranty to remain valid. Ensure these terms are clear and manageable.
Ensuring Quality from Membrane Roofing Manufacturers
To ensure you are getting a high-quality membrane roofing system, consider these factors:
- Reputation of Manufacturer: Choose manufacturers with a solid reputation in the industry. Look for companies with a history of producing high-quality products and positive customer feedback.
- Certifications and Standards: Check if the manufacturer’s products meet or exceed industry standards. Certifications from organizations like ASTM International or the National Roofing Contractors Association (NRCA) can be indicators of quality.
- Material Composition and Thickness: The composition and thickness of the membrane material are critical for its performance and longevity. Thicker membranes often offer better durability.
- Technical Support and Customer Service: Good manufacturers provide strong technical support and customer service, assisting with product selection, installation queries, and warranty issues.
Best Membrane Roofing Provider Companies
Selecting the best membrane roofing provider involves considering factors like product quality, range of options, technological innovation, and customer support. Below are some of the top companies in the membrane roofing industry, each known for specific strengths:
- Firestone Building Products:
- Why: Firestone is renowned for its wide range of high-quality roofing systems, including EPDM, TPO, and PVC membranes. They have a strong reputation for durability and performance, making them a preferred choice for both commercial and residential applications. Firestone’s products are known for their longevity and resilience under various environmental conditions.
- Carlisle SynTec Systems:
- Why: Carlisle is a leader in the roofing industry, especially known for its EPDM roofing systems. They offer a broad selection of membrane roofing options, including TPO and PVC. Carlisle stands out for its focus on sustainability and innovation, often leading the market in environmentally friendly roofing solutions.
- GAF:
- Why: As one of the largest roofing manufacturers in North America, GAF offers a wide range of membrane roofing products, including TPO and PVC systems. They are known for their comprehensive warranty offerings and extensive network of professional installers. GAF’s products are favored for their reliability and quality.
- Johns Manville:
- Why: Johns Manville, a Berkshire Hathaway company, offers a variety of roofing systems, including PVC, TPO, and EPDM membranes. They are recognized for their commitment to innovation, particularly in the area of energy-efficient and sustainable roofing solutions. Their products are well-regarded for quality and performance.
- Duro-Last Roofing, Inc.:
- Why: Duro-Last specializes in custom-fabricated single-ply roofing systems. Their PVC membranes are known for being highly durable and easy to install. One of their key differentiators is their custom fabrication approach, which reduces on-site labor and potential installation errors.
- Versico Roofing Systems:
- Why: Versico is known for its range of single-ply roofing systems, including EPDM, TPO, and PVC membranes. They stand out for their focus on providing total roofing system solutions, including accessories and insulation products. Versico is also recognized for its excellent warranty coverage and training programs for installers.
- Sika Sarnafil:
- Why: Sika Sarnafil is a leading provider of PVC roofing and waterproofing systems. They are highly regarded for their premium quality products and have been used in high-profile projects worldwide. Their roofing systems are known for their longevity and high performance in challenging environments.
Each of these companies has a proven track record in the industry and offers distinct advantages, depending on the specific needs and requirements of the project. When choosing a membrane roofing provider, it’s essential to consider these factors along with local availability, cost, and the specific type of membrane roofing system that is best suited for the project at hand.
Top of Form
Practical Insights and User Guide
Choosing the right membrane roofing material for your property involves considering several factors to ensure you get the most suitable, effective, and cost-efficient roofing solution. Whether for residential or commercial applications, the decision should be based on specific needs, environmental conditions, and long-term goals.
How to Choose the Right Membrane Roofing Material for Your Property
- Assess Roof Slope and Structure: Membrane roofing is ideal for flat or low-slope roofs. Determine your roof’s slope to ensure proper material selection.
- Consider Climate and Environmental Exposures: Different membrane materials respond differently to environmental conditions. For example, if your property is in a region with high UV exposure, a UV-resistant material like TPO might be a better choice.
- Energy Efficiency Needs: If reducing energy costs is a priority, consider reflective or “cool” roofing options like white TPO or PVC, which can lower cooling costs.
- Budget Constraints: While weighing cost, consider both the initial installation cost and the long-term maintenance and energy savings. Sometimes, a higher upfront investment can lead to greater long-term savings.
- Durability and Maintenance Requirements: Evaluate the lifespan and maintenance needs of each material. While some might require more frequent maintenance, others could offer longer durability with minimal upkeep.
- Aesthetic Preferences: Membrane roofing materials come in various colors and finishes. Choose one that aligns with your aesthetic preferences and complements the building’s design.
- Consult with Professionals: Engage with roofing professionals to get tailored advice. They can provide insights based on your specific roof structure, local climate, and building code requirements.
Residential vs. Commercial Applications
- Residential Applications: For residential properties, aesthetic considerations often play a more significant role. Materials like EPDM can be more cost-effective for smaller residential roofs. Additionally, residential properties might require more insulation for energy efficiency.
- Commercial Applications: Commercial roofs often cover larger areas, making the cost per square foot and durability key factors. TPO and PVC are popular in commercial applications due to their durability and ease of maintenance. Commercial roofs might also have more equipment like HVAC units, requiring a more puncture-resistant material.
In both cases, it’s essential to consider the specific requirements and constraints of the property. While residential and commercial roofs share some common considerations, such as the need for durability and weather resistance, the scale and usage of the roof often dictate the most suitable material and installation method.
By carefully assessing these factors and consulting with roofing experts, property owners can make informed decisions that balance cost, performance, and aesthetics, ensuring a roofing solution that meets their needs and stands the test of time.
Maintenance and Lifespan
Maintaining Your Membrane Roof
Proper maintenance is key to extending the lifespan and ensuring the optimal performance of your membrane roof. Regular maintenance not only helps in identifying potential issues before they become major problems but also plays a vital role in upholding the warranty of the roofing system.
Routine Maintenance Tips
- Regular Inspections: Conduct bi-annual inspections, preferably in the spring and fall, to assess the roof’s condition. Look for signs of wear, such as cracks, blisters, or loose seams.
- Debris Removal: Keep the roof surface clean. Remove debris like leaves, branches, and dirt that can accumulate over time and lead to water pooling or block drainage systems.
- Drainage Check: Ensure that drainage systems are clear and functioning properly. Clogged drains can cause water to pool on the roof, potentially leading to leaks and structural damage.
- Surface Wear Checks: Look for any signs of surface wear or damage, especially after extreme weather events. Pay attention to areas around rooftop equipment and penetrations, as these are common spots for leaks.
- Repair Minor Damage Promptly: Addressing small issues promptly can prevent them from escalating into more significant problems.
- Record Keeping: Maintain a log of all inspections, maintenance, and repairs. This record can be valuable for warranty purposes and future inspections.
Repair Guide for Membrane Roofs
- Identify the Issue: Accurately identifying the problem is crucial. Common issues include punctures, seam failures, and membrane shrinkage.
- Choose the Right Repair Method: The repair method depends on the type of membrane and the extent of the damage. For small punctures or tears, patching might be sufficient. Larger issues may require more extensive repairs.
- Patching: For materials like EPDM, this involves cleaning the area around the damage, applying an adhesive, and then placing a patch of the same material over the damaged area.
- Welding for Thermoplastic Membranes: For TPO and PVC membranes, repairs often involve heat-welding a new piece of membrane over the damaged area.
- Professional Assistance: For significant damage or complex repairs, it’s advisable to seek professional help. Improperly executed repairs can lead to further damage or void warranties.
- Regular Follow-Up: After repairs, keep an eye on the area to ensure the problem does not recur.
Regular maintenance and timely repairs are essential for maximizing the lifespan and effectiveness of your membrane roof. By adhering to a consistent maintenance schedule and addressing repairs promptly, you can ensure your roof remains in optimal condition for years to come.
Future Trends in Membrane Roofing
As the construction industry continues to evolve, so does the technology and application of membrane roofing. Staying ahead of the latest trends and advancements is essential for industry professionals and property owners alike, ensuring they make the most informed decisions for their roofing needs.
Innovations on the Horizon
- Eco-Friendly Materials: There is a growing trend towards environmentally sustainable roofing materials. Future membrane roofing products are likely to focus more on eco-friendly manufacturing processes and materials that have a lower carbon footprint.
- Advanced Reflective Coatings: Innovations in reflective coatings for membrane roofs are expected to enhance their ability to reflect UV rays and reduce heat absorption, further improving energy efficiency.
- Integrated Solar Technology: The integration of photovoltaic (PV) cells into membrane roofing materials is an area of keen interest. This innovation could transform roofs into energy-generating assets, especially in commercial and industrial applications.
- Smart Roofing Systems: The development of ‘smart’ roofing systems equipped with sensors to monitor conditions such as temperature, humidity, and structural integrity is on the horizon. These systems could alert property owners to potential issues before they become major problems.
- Improved Durability and Longevity: Research and development efforts are continuously geared towards extending the lifespan of membrane roofing materials, making them more resistant to environmental stressors and wear and tear.
Membrane Roofing in the Next Decade
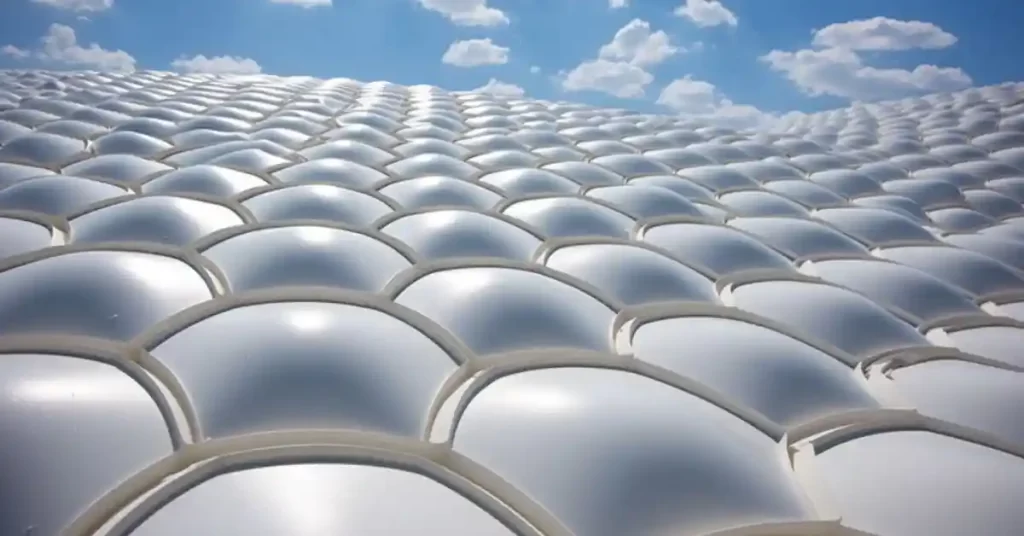
Looking ahead to the next decade, several key themes are likely to define the evolution of membrane roofing:
- Greater Focus on Sustainability: As global emphasis on sustainability increases, membrane roofing materials and practices are expected to become even more environmentally friendly.
- Technological Integration: The incorporation of technology in roofing materials, such as built-in sensors and solar capabilities, will likely become more commonplace.
- Enhanced Performance Standards: With advancements in materials science, the performance standards of membrane roofing materials are expected to rise, offering better weather resistance, longevity, and energy efficiency.
- Customization and Aesthetics: As membrane roofing becomes more popular, expect to see a greater variety in colors, textures, and designs, allowing for more customization to suit different architectural styles.
- Regulatory Changes: Building codes and regulations may evolve to keep pace with these advancements, potentially affecting installation practices and material standards.
In summary, the future of membrane roofing looks bright and promising, characterized by advancements that not only enhance the functional aspects of roofing systems but also contribute positively to environmental sustainability and energy efficiency. Keeping abreast of these changes will be crucial for anyone involved in roofing decisions, from contractors and architects to property owners.
Conclusion
In this comprehensive guide, we’ve journeyed through the multifaceted world of membrane roofing, uncovering its many layers and complexities. From understanding the basic concepts and types of membrane roofing, like EPDM, TPO, and PVC, to comparing them with traditional roofing materials, we’ve explored the essential aspects that make this roofing system a modern marvel in construction.
We delved into the intricacies of installation processes, emphasizing the importance of choosing the right contractor and understanding the associated costs. The discussion about the maintenance and longevity of membrane roofing underscored the significance of regular upkeep in ensuring the roof’s durability and effectiveness over time.
As we looked ahead, the potential future trends and innovations in membrane roofing painted a picture of an industry at the cusp of technological and environmental breakthroughs. These advancements promise not only improved functionality and efficiency but also a commitment to sustainability that aligns with global ecological goals.
In conclusion, the decision to opt for membrane roofing should be made with a comprehensive understanding of its features, benefits, and requirements. This guide aimed to arm you with the knowledge needed to make an informed decision, whether you’re a property owner, a construction professional, or simply someone interested in the evolving landscape of roofing technologies.
Remember, the right roofing choice not only protects your property but also contributes to its aesthetic appeal and energy efficiency. As you move forward, take these insights with you and choose a roofing solution that meets your needs, budget, and long-term goals, ensuring a safe, sustainable, and efficient covering for your valuable space.
Related Article –
- Best Materials for a Flat Roof: Expert Recommendations
- Mastering Commercial Roof Measurement: Techniques and Tools
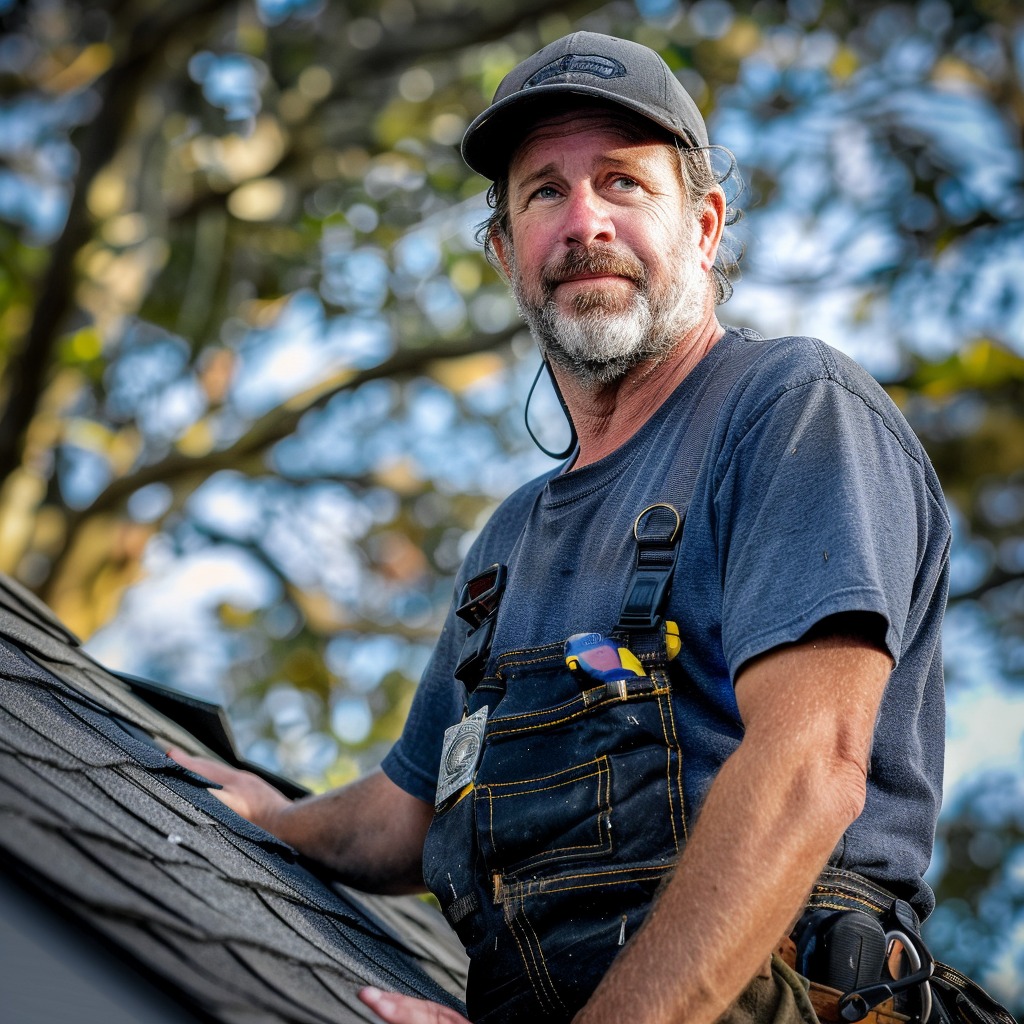
Meet William Adams, a seasoned roofing expert with over 30 years of hands-on experience in the industry. Having worked tirelessly under the scorching sun and through the fiercest storms, William brings a wealth of knowledge and expertise to the table. Hailing from the heart of the USA, he’s witnessed the evolution of roofing practices firsthand, mastering every aspect along the way. Now retired from the field, William spends his days cherishing time with his loved ones while sharing his invaluable insights through this platform. With William at the helm, you can trust that every tip, advice, and recommendation provided is backed by years of real-world experience and unwavering dedication to quality craftsmanship. Join us as we journey through the world of roofing, guided by the wisdom and passion of a true industry veteran.